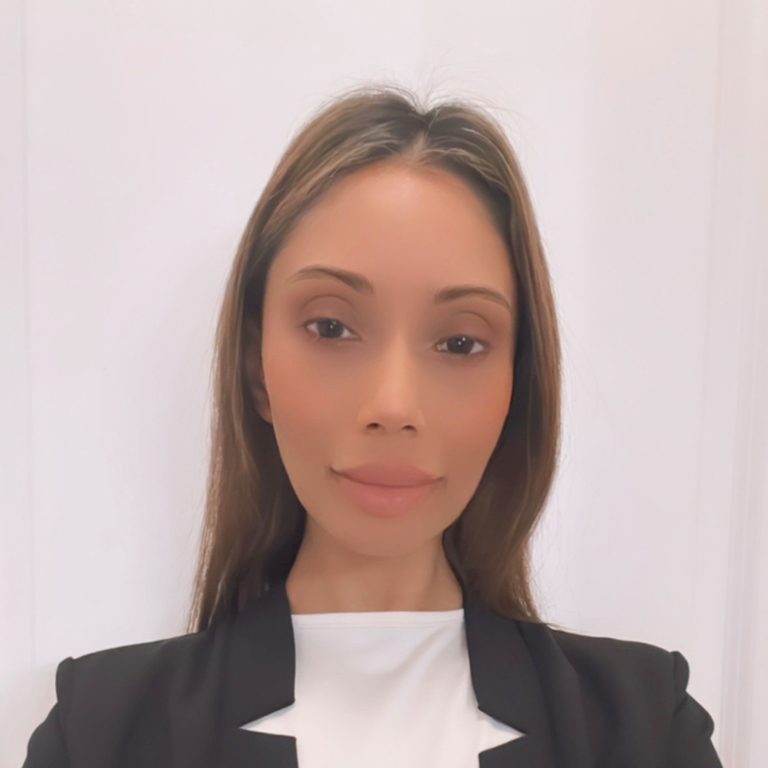
Par Trisha Sirju ,
Vice-président et consultant principal en prévention des sinistres, Marsh Services-conseils
05/10/2024 · Lecture de 5 minutes
En tant qu’entreprise, vous comprenez le rôle crucial que joue l’équipement dans les environnements industriels. Vous comptez sur ces biens pour rationaliser les opérations et améliorer la productivité. Cependant, lorsque des dysfonctionnements inattendus se produisent, les conséquences peuvent être désastreuses. Ils peuvent perturber les processus de production, provoquer des retards et entraîner des pertes financières importantes. Il est donc essentiel de prioriser l’exploitation et la manipulation sécuritaires de l’équipement pour assurer le bien-être des employés, protéger la continuité des activités et atténuer les risques. Heureusement, en mettant en œuvre des pratiques exemplaires, comme la formation des employés et la maintenance proactive, les entreprises peuvent résoudre rapidement les dysfonctionnements de l’équipement et en minimiser les conséquences.
Pour assurer le bon fonctionnement de l’équipement et minimiser les interruptions, il est important de connaître les formes courantes de mauvais fonctionnement de l’équipement. Des facteurs tels que les conditions environnementales, l’utilisation de l’équipement, les fortes vibrations et l’exposition à des produits chimiques agressifs peuvent contribuer à la gravité des défaillances de l’équipement.
Voici quelques-uns des types de mauvais fonctionnement de l’équipement les plus courants que toute entreprise doit connaître afin d’aborder et de résoudre les problèmes, d’améliorer la gestion de l’équipement et d’améliorer la sécurité en milieu de travail :
En étant conscientes de ces types courants de mauvais fonctionnement de l’équipement, les entreprises sont mieux à même de prendre des mesures pour prévenir et résoudre les problèmes, garantissant ainsi des opérations plus fluides et minimisant les temps d’arrêt.
Risques associés à la défaillance de l’équipement
Pour contribuer à atténuer les risques mentionnés ci-dessus, il est essentiel de suivre les pratiques exemplaires décrites ci-dessous :
Respecter les instructions du fabricant : il est essentiel de respecter rigoureusement les instructions du fabricant pour prévenir les pannes de machine. Les techniciens et les opérateurs doivent lire attentivement les manuels et suivre les instructions qui y sont fournies. Ces instructions comprennent généralement des exigences d’étalonnage, des listes de vérification, des conseils de dépannage et d’autres renseignements importants pour un fonctionnement sécuritaire et efficace.
Assurer une formation continue : l’erreur humaine peut contribuer aux pannes des machines et aux problèmes de sécurité. L’équipe responsable de l’entretien de l’équipement doit avoir une connaissance approfondie des composants des machines, tandis que le personnel doit être formé à l’utilisation sécuritaire et efficace de toutes les machines qu’il utilise. Des séances de formation régulières doivent être organisées pour tenir les employés informés des mises à niveau ou des modifications apportées à l’équipement. La formation continue contribuera à préparer le personnel à être efficace et performant en matière de sécurité et de manipulation de l’équipement.
Éviter de trop solliciter l’équipement : chaque machine a ses limites et le fait de trop solliciter un équipement peut entraîner des pannes, une surchauffe et une réduction de sa durée de vie. Il est important de s’assurer que les charges de travail imposées aux machines ne dépassent pas leur capacité maximale. S’il est nécessaire d’atteindre des quotas ou d’augmenter la production, envisagez d’investir dans un nouvel équipement plutôt que de surmener les machines existantes.
Établir une liste de contrôle complète : une liste de contrôle complète est essentielle pour réduire au minimum les temps d’arrêt imprévus et les défaillances fréquentes. Rédigez une liste de contrôle qui couvre toutes les inspections nécessaires afin de garantir la détection et la résolution immédiates des problèmes potentiels. Incluez des éléments tels que les dispositifs de sécurité de l’équipement, les composants électriques et le câblage, les points de lubrification, la tension des courroies et un inventaire des pièces de rechange.
Effectuer une maintenance proactive : l’adoption d’une approche de maintenance proactive est plus rentable que la maintenance réactive. La maintenance proactive consiste à surveiller l’environnement et l’état des machines, ce qui permet de régler les problèmes mineurs avant qu’ils ne deviennent des problèmes majeurs. Une stratégie proactive réduit la probabilité de pannes inattendues et contribue à garantir des opérations plus fluides.
L’exploitation et la manipulation sécuritaires de l’équipement de la machinerie lourde sont d’une importance capitale. Des mesures proactives peuvent contribuer à assurer le bien-être des employés, à maintenir l’efficacité opérationnelle et à préserver la stabilité financière et la réputation de l’organisation. En reconnaissant l’importance d’une exploitation et d’une manipulation sécuritaires, les entreprises peuvent contribuer à créer un environnement de travail sûr et productif tout en atténuant les conséquences potentielles des bris d’équipement.