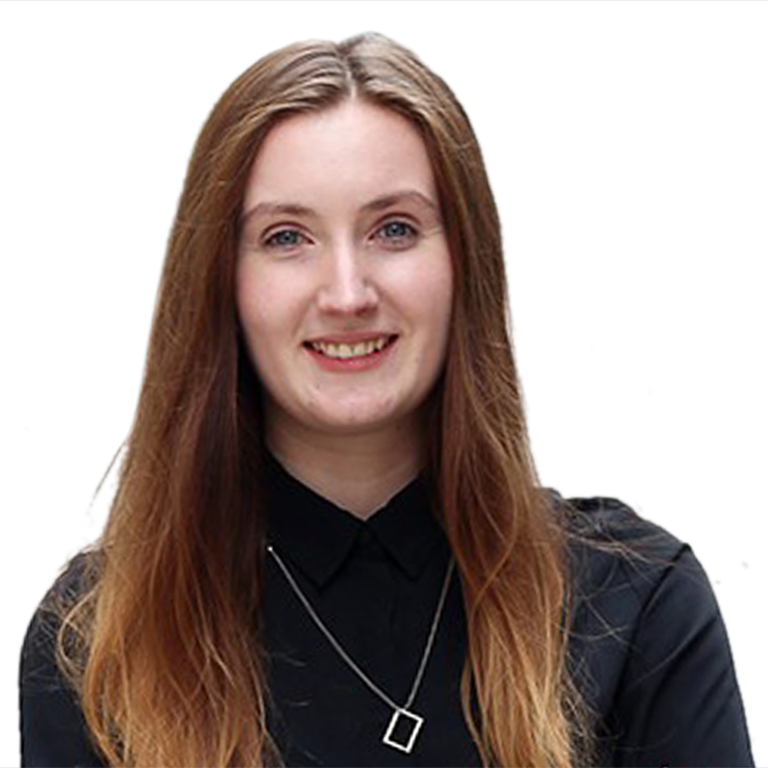
By Jenni Morrison ,
Risk data analytics specialist
06/02/2024 · 6 minute read
The energy industry operates on a delicate balance of progress and risk. Major incidents and losses can have far-reaching consequences, some of which could have been prevented had the root cause been addressed. Analyzing, reviewing, and learning from incidents and others’ experiences can help organizations strengthen their risk management practices and plans.
To build and maintain resilient and sustainable operations, organizations need to avoid risk complacency in order to ensure the safety and well-being of their workforce, communities, environment, and their long-term financial viability. The repercussions of ignoring risk recommendations can range from reputational damage to financial loss and, in the worst-case scenario, loss of life. Failure to address identified risks erodes the trust stakeholders place in an organization's ability to operate with integrity and purpose.
Risk management practices in the energy and power industry have continued to improve largely driven by structural dynamics such as digitalization and regulation, as well as advanced operational awareness and procedures. But eliminating or at least reducing bias remains one of the most important actions to integrate into operational and strategic risk reviews. Biases often operate subconsciously and can lead to irrational or uninformed decision-making, increasing rather than reducing risk. By understanding the known biases, and uncovering some of the imperceptible ones, companies can develop a culture of awareness, agility, and vigilance.
Several common themes emerge in relation to major loss incidents, primarily relating to process safety management: culture, cost, and compliance. These factors can influence the level of success in learning from past incidents, or in taking action on learnings effectively over time and across multiple sites.
Culture is a big factor and sometimes overlooked when assessing risk. Checklists, documented procedures, and technical know-how can be compromised without a mature process safety culture that is woven into the fabric of an organization’s psychology.
While personal safety is essential, focusing solely on it can lead to a skewed perception of overall safety. For instance, many companies measure process safety performance with personal safety indicators, such as the safe number of hours worked. The US Chemical Safety and Hazard Investigation Board (CSB) found that only measuring personal safety-related KPIs can provide a false sense of safety to organizations, which can inflate their risk tolerance. Or worse, it can breed complacency rather than drive towards building team culture and shared, enterprise-wide, purpose-aligned goals.
A common misconception in the energy industry is that the traditional benefit-cost approach may only partially justify investments in reducing exposures to low-probability, high-consequence events. In a risk-based operational environment, it is crucial to strike a balance between financial considerations and the imperative to prevent catastrophic incidents. Alternative approaches, such as real-time monitoring and control systems, that prioritize process safety without solely relying on traditional benefit-cost analyses can provide a more comprehensive evaluation of risk management investments.
Beyond financial implications, the reputational damage caused by ignoring risk recommendations can be devastating. Stakeholders including customers, investors, and the public, expect organizations to prioritize safety and responsible practices. Failing to heed risk warnings undermines trust, tarnishes brand image, and can have long-term consequences for business relationships and market standing.
Neglecting recognized risks can also lead to regulatory non-compliance and legal violations, including criminal charges in the most extreme cases. The energy industry is highly regulated to promote adherence to safety guidelines designed to protect workers, the environment, and the public.
The 100 largest losses detailed in this report illustrate that lessons from prior incident investigations did not always spark action and better prevention steps. Some of the most significant risk management themes for the energy industry are evidenced in a few examples below.
The Piper Alpha loss remains the costliest recorded property damage loss.
An audit before the explosion had identified shortcomings in maintenance and safety procedures on the rig. The audit recommended the installation of a valve to isolate a specific section of the pipeline in the event of a fire, and the implementation of a lockout tagout (LOTO) procedure. The recommendations were not actioned.
In 2017, a similar root cause led to a major loss in the UAE. This incident was linked to a lack of proper control of isolation, a lesson and engineering requirement that could have been applied after Piper Alpha.
A risk assessment had indicated significant deficiencies in the depot's overfill prevention systems. No action was taken, and a massive explosion led to extensive damage to the depot, nearby properties, and the environment.
The American Petroleum Institute (API) made changes to the Tank Overfill Prevention Standard, API 2350, which outlines best practices for preventing tank overfills in petroleum facilities. Despite this, some companies may not have yet applied the necessary overfilling protection hardware and system measures.
To date, this is the largest marine oil spill in history.
Prior to the incident, risk improvement recommendations were identified for the integrity of the well's cementing and the functionality of the blowout preventer. The work was not commissioned due to the significant cost, and the consequences of a failure were grossly underestimated.
Risk perception and risk tolerance highlight the need for a balanced approach to decision-making and budgeting that considers short-term gains and long-term safety implications.
Three years before the incident, a process hazard analysis (PHA) identified the risk of popcorn polymer buildup in dead legs. The PHA proposed flushing the lines monthly to prevent any potential accumulation and localized corrosion.
The operator did not follow through with the recommendation, due in part to cost concerns. The monthly flushing was considered unwarranted as the risk of polymer build-up was perceived to be low. An investigation by the US Chemical Safety Board (CSB) revealed that ignoring risk recommendations significantly contributed to the explosion.
This incident underscores the critical importance of acting on risk recommendations, as seemingly small decisions can have far-reaching consequences.
History has demonstrated that the industry can continue to improve its efforts at addressing recognized hazards and proactively implementing risk improvement recommendations.
The key takeaways from these incidents are clear:
Prompt action: Operators must address known risks without delay, and risk improvement recommendations should be implemented as soon as practical to mitigate potential hazards.
Effective communication: Clear communication among stakeholders, including risk engineers, operational personnel, and management, is essential to ensure that identified risks are effectively understood and actioned.
Compliance and oversight: Regulatory compliance and rigorous change management oversight are necessary to implement risk improvement recommendations and promote the safety and integrity of operations.
Continuous improvement: A culture of continuous improvement, aligned to shared goals should be fostered within an organization - and across the energy industry - encouraging regular review and reassessment of risk management practices.
By investigating and learning from operational incidents, organizations can strengthen risk management practices, minimize losses, protect the environment, and safeguard the well-being of people and property. Through a collective commitment to proactive risk management the industry as a whole can become more resilient.