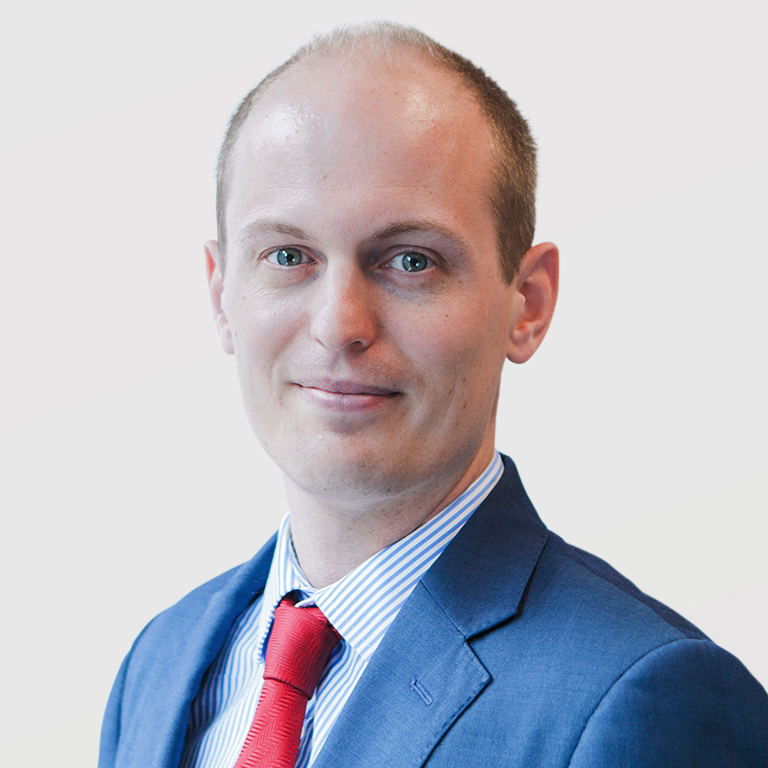
Hugh Waggett
Advisory Quality and Recall Leader, Marsh Advisory
Recent data reveals that European automotive recalls increased 17.7% in 2021 and by 31.7% in 2022 – reaching a figure more than double above the annual industry average of the last 16 years. It is critical organisations in the automotive industry are prepared ahead of potential recall events.
The last 10 years saw injuries remain the leading annual cause of European automotive recalls, while fire risk recalls have increased by 29.9% since 2020. Additionally, manufacturers have been faced with billion-pound fines and criminal negligence charges for the alleged “covering up” of faults.
Furthermore, as electric vehicle (EV) sales increase, so too have recall notices. One manufacturer initiated a recall of over 14,000 EVs for faulty battery software, while another original equipment manufacturer (OEM) recalled 49,000 EVs over concerns that a safety defect might render the vehicle immobile. While these are two more pertinent, recent examples, other EVs have been recalled over various software bugs, battery fire risks, and other minor issues.
Newer technical complexities and a highly competitive market pushing manufacturers to hastily launch new vehicles are partly responsible for the marked rise in recall incidents.
Although the international sourcing of components is now an industry standard mode of operation, it can still present significant risks for OEMs and large suppliers. Buying items and input materials in the global marketplace can lead to conflicts over the necessary quality thresholds and achieving the lowest cost.
Many OEMs purchase goods without detailed knowledge of each individual supplier, let alone the capability to audit quality controls and traceability processes. Therefore, it becomes difficult to identify if an unscrupulous supplier is using cheap, inferior, or counterfeit materials that could potentially be the root cause of a specific fault responsible for a vehicle recall.
Despite best efforts, unsafe products can circumvent quality management controls and enter the marketplace. Recalls present a real threat to organisations through loss of sales, erosion of customer confidence, or damage to public health. Preparation is critical for car manufacturers to be responsive to a product recall. This enables sufficient protection for their brand, corporate reputation, and balance sheet.
Four common issues periodically impede organisations dealing with product recalls. Process and governance, information management, stakeholder management, and resourcing are topics that all parties would benefit from regularly discussing.
Roles and responsibilities for addressing product quality – including the decision to action recalls – should be both structured and suitably adaptable to handle complex situations as they arise. Common weaknesses include: poor clarity of crisis response duties, inefficient cross-functional cooperation, missed opportunities, and delays to decision-making. This can make an organisation appear apathetic to both affected customers and the media.
Traceability of affected products, along with the locating of relevant technical and procedural documentation, needs to occur quickly. Reliable recording of key decisions, tracking performance, and cost metrics are also essential for businesses to understand the financial cost of a recall event. Poor performance can result in failure to properly satisfy regulators and shareholders that all affected product is located and accounted for. Difficulty in managing costs or scope of remediation efforts can make loss recovery from insurers complicated.
Transparent and consistent communication – internally and externally – is vital to ensuring effective mitigation of reputational damage. The perception of dishonesty and inconsistency within organisations can undermine stakeholder confidence – potentially exacerbating a crisis beyond the original product issue.
Upon discovery of a fault, it is essential resources are mobilised rapidly to categorise the cause and scope of the issue. This facilitates a swift design and implementation of a technical solution. Identification and engagement of knowledgeable experts – with relevant experience – in short timeframes can also enhance the effectiveness of responses. However, increasing customer-facing resources to meet the inevitable surge in demand can pose difficulties and therefore should be planned for in advance.
Being recall ready ensures that your organisation has the people, processes, and experience for an effective response. This is achievable through the following actions:
Product recalls can be extremely costly for organisations operating within the automotive industry. Manufacturers and suppliers in this space need to consider the financial impact a recall event could have on their balance sheet, brand, and reputation.
Identifying risks early and mitigating against potential incidents ensures that you are better prepared in the event of a recall.
To find out how Marsh can further support your organisation’s efforts to become recall ready, please contact your Marsh representative.
Advisory Quality and Recall Leader, Marsh Advisory
Marsh UK Industries - Automotive & Manufacturing Industries Leader
United Kingdom
Product Recall Broker