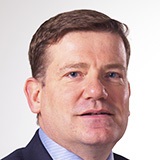
By John Cooper ,
Global Chief Client Officer, Energy & Power, Marsh Specialty
04/29/2022 · 6 min read
The report provides an opportunity to revisit lessons from the past, and identify key issues and trends from large losses, to understand improvements to operations and risk management practices.
There were only two new additions to the largest 100 ranking since our last report in 2020, with property damage costs of US$200 million and US$300 million respectively. This equates to the lowest average amount for any two-year period in the 100LL ranking since 1995/96 (see Figure 1). This is a remarkable change compared to the last few editions of the 100LL publication with 2018/19 contributing seven entries (totaling US$4.1 billion); 2016/17 contributing four entries (totaling over US$2.6 billion); and, 2014/15 contributing three entries (totaling US$1.4 billion).
The relatively low amount of US$250 million per year for 2020/21 is highlighted for ease of reference (orange line).
From a process safety perspective, the pandemic may have indirectly helped in the short-term. However, the medium to long-term impact remains to be seen.
The swift flurry of major losses that some feared at the start of the pandemic did not materialize. This is partly due to sites successfully managing the disruption to established work practices through well-executed business continuity plans. This included changes to staffing levels and management of associated fatigue risk for shift workers. There are also a number of factors that may have helped to mitigate potential process safety risks:
Moving forward, there are a number of potential risks that will need to be carefully managed to prevent potential “delayed losses”. Operators should consider the following:
Seven property damage losses associated with gas processing feature among the 100 largest losses — the most recent was a fire that occurred in Norway in September 2020.
The properties of LNG mean that the risk of internal corrosion is greatly reduced and significant global experience with the design, construction, and operation of LNG facilities has helped contribute to the relatively limited incidents of very large losses in this sector. The September 2020 fire reportedly occurred because, “the anti-icing heat exchanger in the air inlet was used outside of its intended area of application.”[i] This serves as a reminder that the potential does exist for high-consequence losses in this sector due to their complexity and value.
There have been no new additions to the 100LL from this sector over the last two years. However, there have been some notable petrochemical losses, including two in South Korea: Daesan in March 2020 and Yeosu in November 2020.
Although it doesn’t qualify for the 100LL, a major explosion at a petrochemical plant in Tarragona, Spain, in January 2020 resulted in three fatalities. One of these fatalities occurred several kilometers from the site, caused by a one-metric ton projectile. This demonstrates the potentially significant third-party liability exposures for this sector.
A number of factors contribute to petrochemical plant loss history. They often contain a concentration of high-value equipment and machinery, typically operate at high temperatures and pressures, and require the careful control of potentially violent chemical reactions. However, materials processed at petrochemical plants have normally been pre-processed (for example, supplied by oil refineries), meaning that most contaminants in the feedstocks will have been removed prior to receipt, making them less susceptible to several corrosion mechanisms.
One new refinery loss was added to this edition of the 100LL, and refinery losses now make up 37% of the largest losses. The incident occurred in Cape Town, South Africa, in July 2020.
In general, oil refineries are a group of aging assets. Older assets have often been subject to both expansion projects to increase capacity, and retrospective installation of high-value, high-conversion assets. Together these have resulted in higher concentration of value at sites. Refineries process crude oil and therefore, have a far more dynamic and broad feedstock range than the other asset classes.
The combination of aging assets, increased concentration of value, and diverse feedstocks, are all likely to have contributed to the fact that this sector makes up the largest proportion of the 100LL.
Only seven losses associated with terminal and distribution operations feature among the 100LL; the most recent occurring in 2005. The physical layout of most terminal and distribution assets, coupled with the value of the plant and its equipment, means that few sites have enough concentration of value to result in the very largest physical damage losses.
The upstream sector accounts for 23% of the 100LL. However, it’s important to remember that the report only covers property damage, and does not include the additional costs of good control, or third-party liability. The total third-party liability claims for the Macondo loss in the Gulf of Mexico in 2010, are understood to be more than 40 times the value of the associated property damage loss.
The most recent upstream loss to be included in the 100LL occurred in February 2016 and the five subsequent years mark the longest period without an upstream addition to the 100LL ranking since the period 1993 to 2001.
[i] Investigation of the fires at Tjeldbergodden and Hammerfest now concluded
Article
10/26/2021